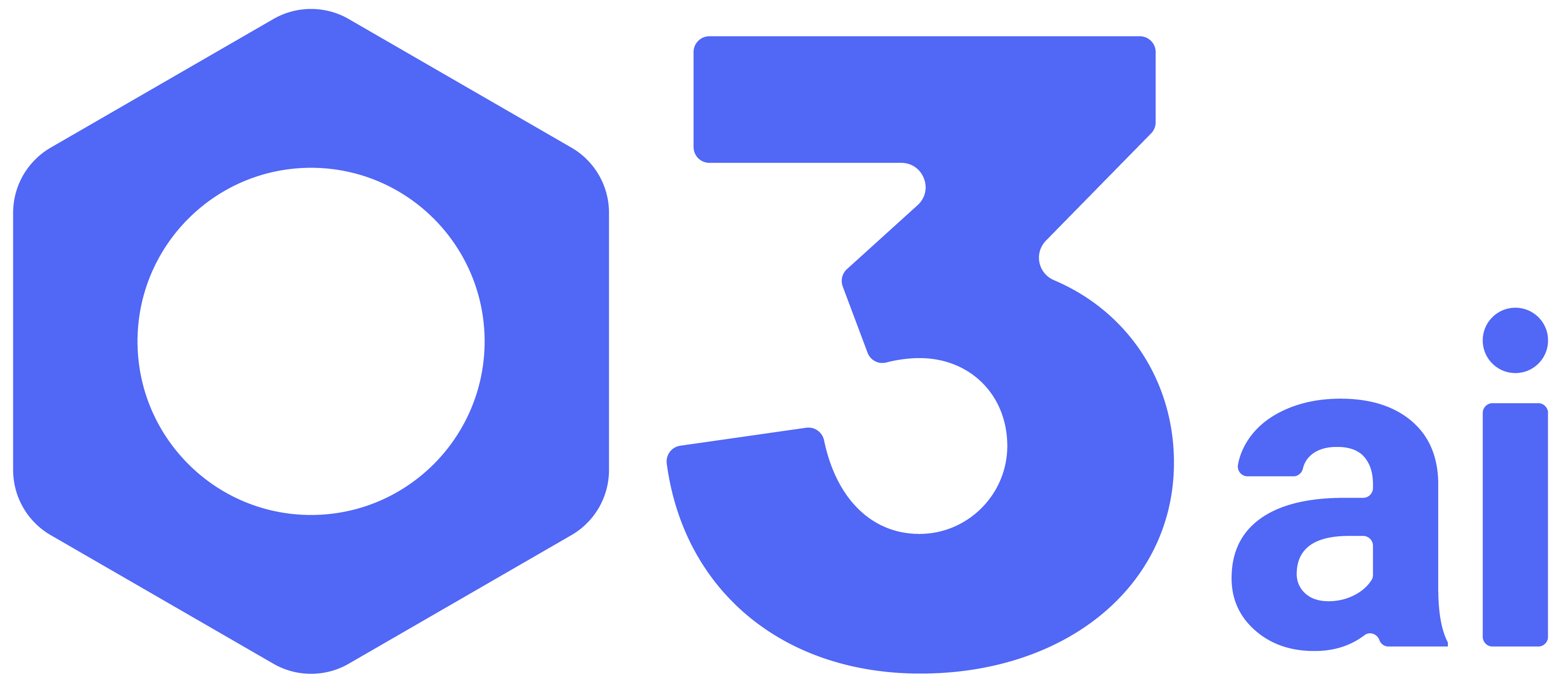
Make Your Factory Lean With O3ai
info@o3ai.com
+41 79 542 92 56
+966 563 985 430
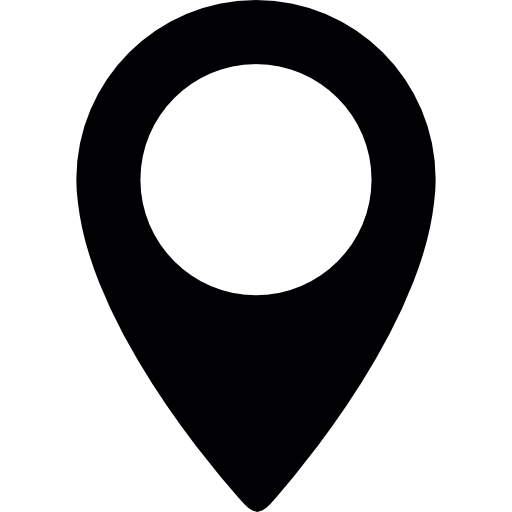
Riyadh, Saudi Arabia
In today’s hyper-competitive manufacturing landscape, companies are constantly seeking ways to optimize operations, reduce costs, and improve quality. While technological advancements like automation, artificial intelligence, and IoT have revolutionized production processes, the human element of decision-making remains critical. One of the most effective tools for aligning human efforts with organizational goals is Key Performance Indicator (KPI) management. When implemented strategically, KPIs can serve as a compass, guiding manufacturers toward sustained success.
This article explores how KPI management can be leveraged to drive manufacturing performance, offering actionable insights and real-world examples that demonstrate its transformative potential.
At its core, KPI management involves identifying, tracking, and analyzing metrics that directly impact business objectives. In manufacturing, these metrics often revolve around productivity, efficiency, quality, safety, and cost control. However, simply monitoring numbers isn’t enough. To truly drive performance, KPIs must be:
When these principles are applied, KPIs become more than just numbers—they become catalysts for change.
Efficiency is the lifeblood of any manufacturing operation. By tracking KPIs such as Overall Equipment Effectiveness (OEE), cycle time, and downtime frequency, manufacturers can pinpoint inefficiencies and implement targeted improvements. For example:
Quality issues can erode customer trust and lead to costly recalls. KPIs like defect rates, first-pass yield, and scrap percentage help ensure products meet stringent standards. Consider this scenario:
People are at the heart of every manufacturing process. KPIs related to workforce productivity, training completion rates, and incident reports foster a culture of accountability and safety. For instance:
In an era of global supply chains, visibility is paramount. KPIs such as order fulfillment time, inventory turnover, and supplier lead times enable manufacturers to anticipate bottlenecks and respond proactively.
As environmental concerns grow, sustainability has become a competitive differentiator. KPIs like carbon emissions per unit, water usage, and waste reduction targets help manufacturers align with regulatory requirements and consumer expectations.
To maximize the impact of KPIs, manufacturers must adopt best practices that ensure clarity, consistency, and continuous improvement:
Consider the case of a mid-sized automotive parts manufacturer struggling with declining profitability. After implementing a robust KPI management system, the company identified several pain points:
By focusing on KPIs such as defect rate reduction, OEE improvement, and labor cost optimization, the company achieved remarkable results:
Within two years, the plant not only regained profitability but also earned recognition as one of the top-performing facilities in its parent organization.
KPI management is more than a buzzword—it’s a strategic framework that transforms raw data into actionable insights. For manufacturers, it represents an opportunity to align every aspect of their operations with overarching goals, ensuring resilience in the face of challenges and agility in seizing opportunities.
However, the true magic of KPIs lies not in the numbers themselves but in the behaviors they inspire. When employees see how their daily efforts contribute to measurable progress, they become invested in driving success. And when leadership uses KPIs to communicate vision and celebrate achievements, a culture of excellence naturally emerges.
In the quest for manufacturing excellence, KPI management isn’t just a tool—it’s a mindset. Embrace it, refine it, and watch your organization soar to new heights.
Find out what O3ai can do for your factory – get in touch today..