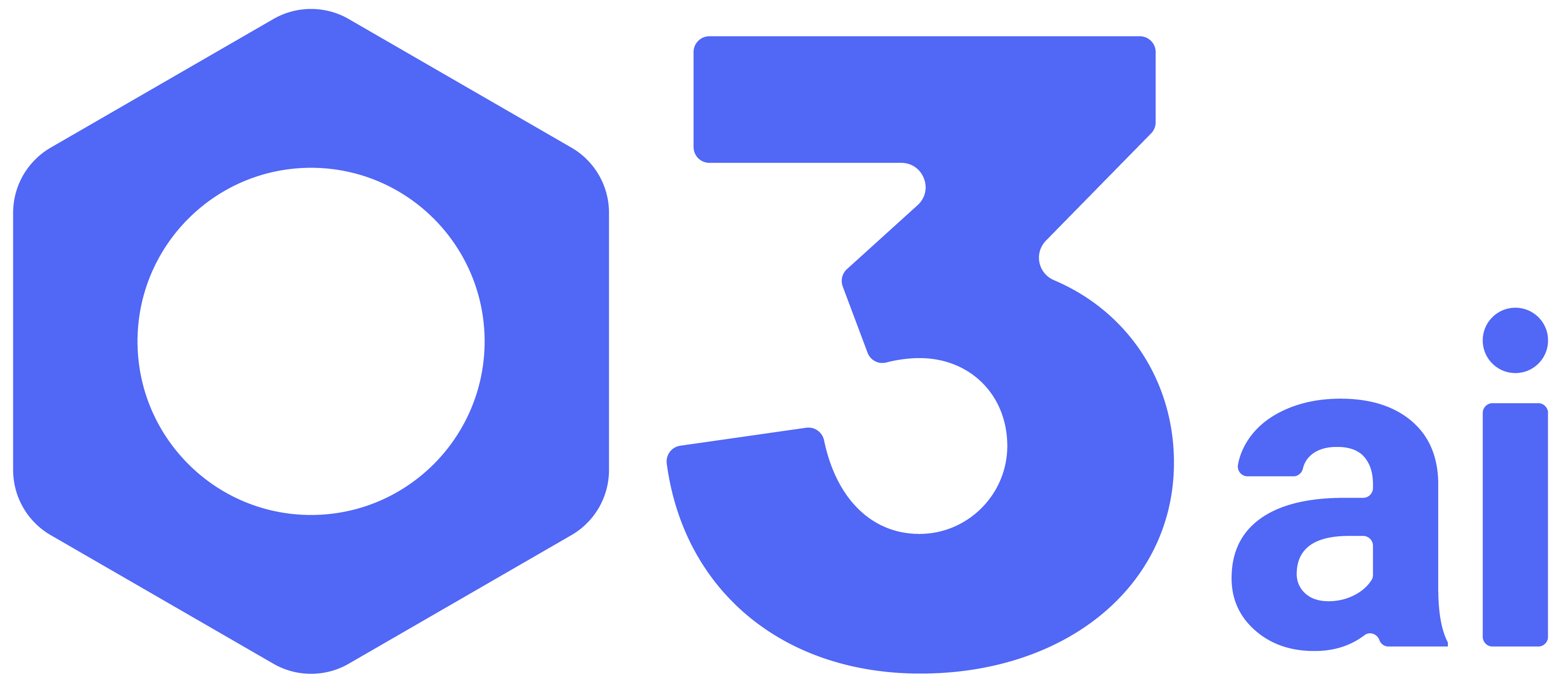
Make Your Factory Lean With O3ai
info@o3ai.com
+41 79 542 92 56
+966 563 985 430
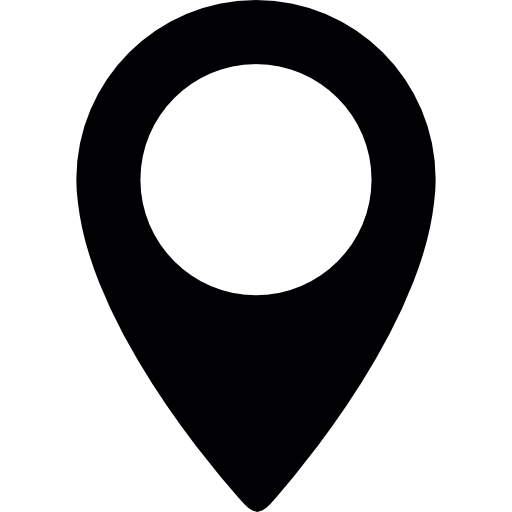
Riyadh, Saudi Arabia
Unless you’ve been hiding under a rock for the past decade, you’ll have heard of Industry 4.0 and the evolution of smart factories.
Industry 4.0 represents a shift towards merging digital technology and physical manufacturing processes and activities. The meeting and unification of information technology (IT) and operations technology (OT) has given rise to smart factories.
In a nutshell, a smart factory is a fully connected, highly automated, and flexible manufacturing facility. Smart factory technology is proving to be highly beneficial for manufacturing companies, with some reporting production output and labor productivity gains of between 10 and 12%.
Automation has been a feature of factories for a very, very long time and it goes back to the years before our era, with the humble water wheel appearing in 400 BCE to automate the milling process. However, until the 21st century, the focus was on mechanized automated machinery. The digital era has changed everything.
The term “fourth industrial revolution” or Industry 4.0 was coined to describe the increase in connectivity between machines, devices, and people, and the increased use of data to inform decision making and business direction.
The aim of transitioning from a traditional factory to a smart factory is to streamline operations through increased automation, enhance decision making through the increased use of data-driven digital tools, and improve outcomes across the entire manufacturing value chain.
Implementing smart factory enhancements can help manufacturing companies to:
A frequent concern among manufacturing companies is whether to make the move to smart factory technology now or wait to see how things progress. Emerging Industry 4.0 trends suggest that now is the time to adopt smart factory technology for the following reasons:
Smart manufacturing involves the implementation of three main elements.
IIoT refers to the interconnected nature of industrial machinery and devices through data exchange networks. The data communication systems typically transfer data points from device sensors with cloud-based platforms and storage.
Specialist sensors are attached to machinery and devices at key stages to provide the data points required for real-time insight generation and decision making. For example, temperature sensors positioned in a plastic injection molding machine can help to optimize the production process of plastic goods.
The data flows from IIoT sensors and devices to cloud storage and cloud-based software. A typical smart manufacturing platform, such as O3ai, will store all the collected data securely in the cloud and automatically apply advanced data analysis tools. The analysis is designed to spot patterns, potential bottlenecks, maintenance issues, and generate valuable insights with a high degree of accuracy.
If you’re thinking about implementing smart manufacturing technology to enhance your operations, it’s best to start small and slowly, then scale up fast. Staying agile and flexible in your approach will help you to find the right fit for your specific requirements.
Running a pilot project is recommended, as it allows you to test and trial different technologies in a small controlled environment and monitor the results carefully. Once you are satisfied that the implementation will consistently produce positive outcomes, you can roll out the technology across your operations and scale up at pace.
Here at O3ai Smart Manufacturing, we can help you to identify key areas that would benefit from digital solutions and IIoT technology.
Our no-code cloud-based modular platform is ideal for manufacturers that are starting out with smart technology as you can add single modules at a time and scale up rapidly when the time is right.