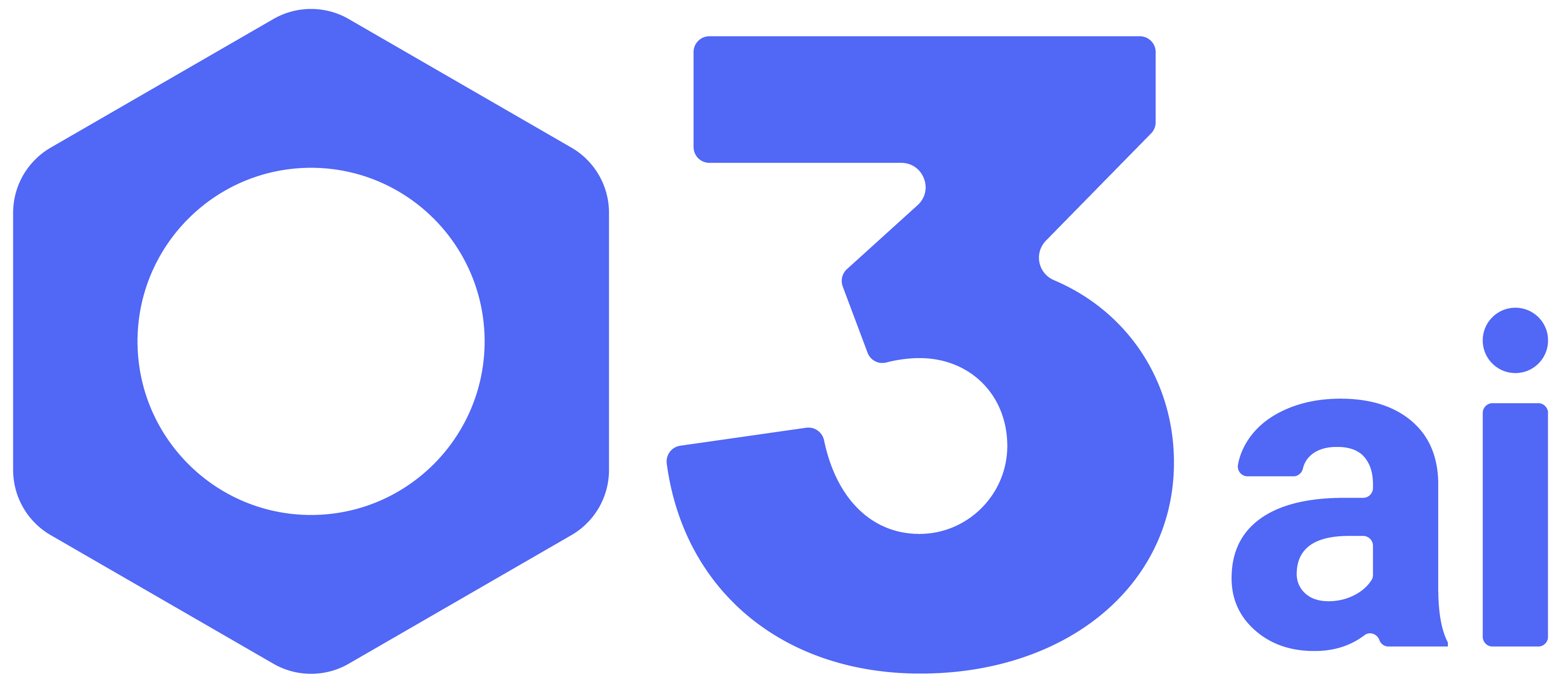
Make Your Factory Lean With O3ai
info@o3ai.com
+41 79 542 92 56
+966 563 985 430
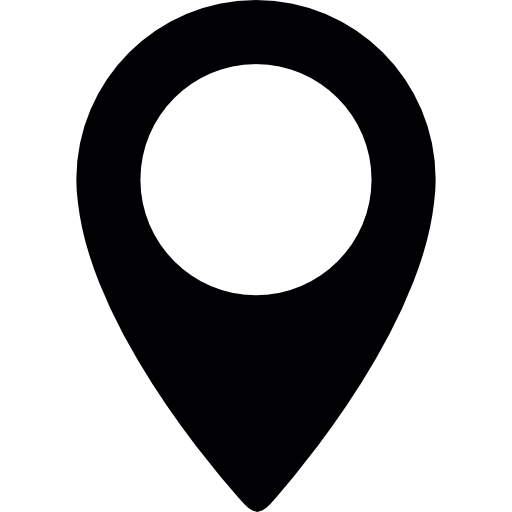
Riyadh, Saudi Arabia
“Proactive maintenance strategies that leverage real-time data and predictive analytics can reduce unplanned downtime by 30-50%, improving overall asset efficiency.”, according to McKinsey. Understanding Mean Time to Repair (MTTR) and Mean Time Between Failures (MTBF) is critical for organizations aiming to optimize their maintenance strategies and enhance operational resilience.
These two key performance indicators (KPIs) provide insights into equipment reliability, repair efficiency, and overall asset performance. By leveraging MTTR and MTBF effectively, manufacturers can shift from a reactive to a predictive maintenance model, reducing disruptions and boosting productivity.
According to Deloitte, “Companies that use advanced maintenance analytics, including failure predictions and automated workflows, experience a 20-30% increase in equipment uptime and significant cost reductions.” Optimizing MTTR and MTBF helps businesses:
McKinsey estimates that predictive maintenance can reduce equipment breakdowns by 50% while lowering maintenance costs by 10-40%. By integrating IoT sensors, AI-driven analytics, and historical maintenance data, manufacturers can detect failure patterns and intervene before breakdowns occur.
Example:
An automotive plant integrated IoT-enabled vibration monitoring for its assembly line robots, allowing maintenance teams to address potential failures 48 hours before they occurred, reducing unplanned downtime by 30%.
Automated maintenance systems streamline scheduling, task assignment, and response times, reducing MTTR significantly.
Key Actions:
Empowering frontline workers to handle minor repairs reduces the time required for external technicians to intervene.
Key Actions:
A lack of essential spare parts can increase MTTR due to extended repair times.
Solution:
Tracking MTTR & MTBF trends over time allows organizations to set performance benchmarks and identify areas for improvement.
Key Actions:
A global electronics manufacturer struggled with frequent breakdowns on its high-speed assembly lines. By leveraging MTTR & MTBF analytics, the company:
Understanding and optimizing MTTR & MTBF is no longer optional—it’s essential for manufacturers aiming to reduce downtime, improve efficiency, and lower costs. As PwC states, “Organizations that embrace digital maintenance strategies achieve up to 15% cost savings while increasing asset reliability.”
By adopting predictive analytics, automation, and proactive maintenance planning, manufacturers can turn maintenance from a cost center into a strategic advantage. Investing in these strategies not only improves machine reliability but also strengthens an organization’s ability to compete in an era of smart manufacturing and Industry 4.0.
O3ai provides a cutting-edge AI-driven maintenance optimization solution that helps manufacturers reduce downtime and increase asset reliability. By integrating predictive maintenance, IoT-enabled real-time monitoring, and automated repair workflows, O3ai ensures that companies achieve lower MTTR, higher MTBF, and maximum operational efficiency.
✔ AI-Powered Predictive Maintenance – Detects anomalies and predicts failures before they occur, reducing unexpected breakdowns.
✔ Automated Workflows & Real-Time Alerts – Streamlines maintenance scheduling and response times for minimal downtime.
✔ Comprehensive Equipment Health Monitoring – Provides data-driven insights on asset performance and optimization opportunities.
✔ Seamless Integration with Existing Systems – Connects effortlessly with MES, ERP, and CMMS platforms.
✔ Scalable & Cloud-Enabled – Ensures visibility across multiple production sites with centralized control.
By leveraging O3ai’s intelligent maintenance tools, manufacturers can achieve industry-leading reliability, maximize asset performance, and drive continuous improvement—ultimately ensuring that downtime is reduced and productivity is optimized.
Want to see how O3ai can transform your maintenance strategy? Get in touch today!