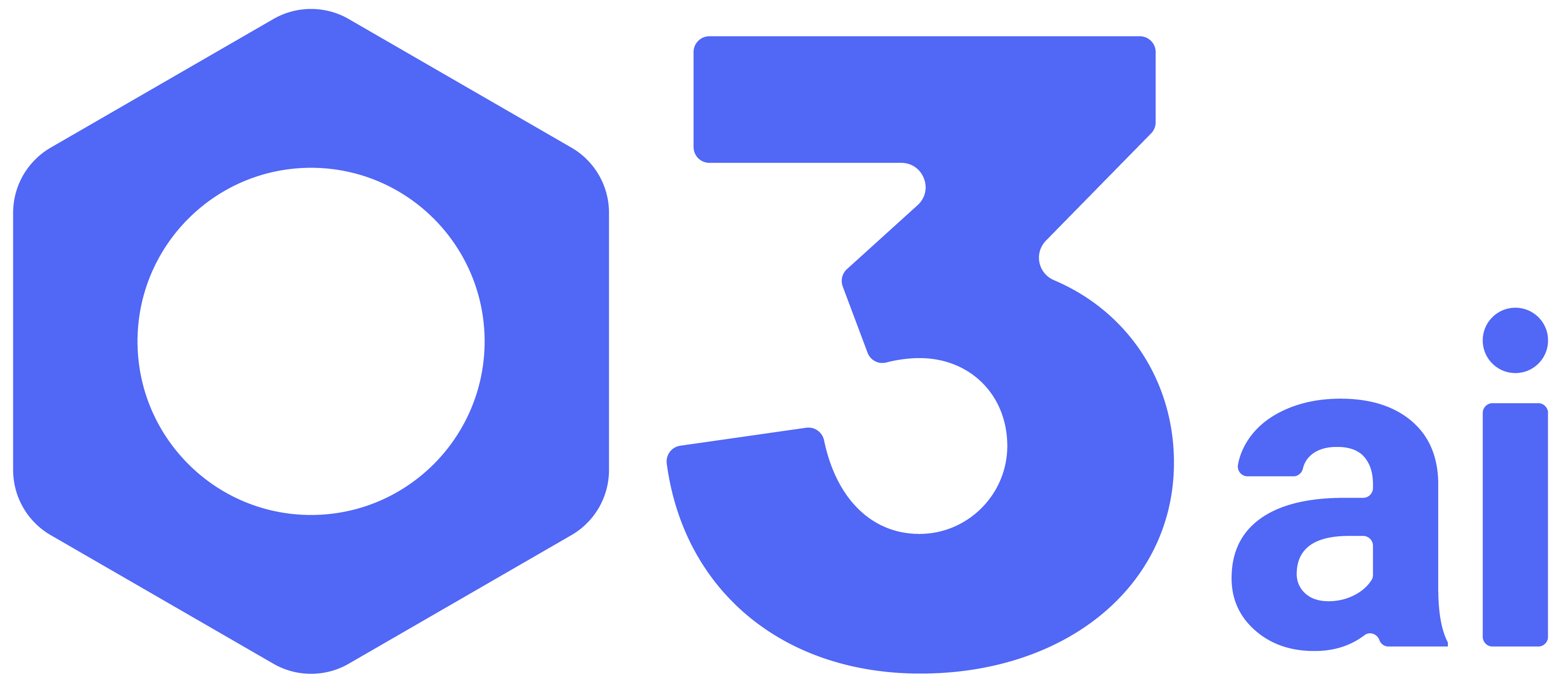
Make Your Factory Lean With O3ai
info@o3ai.com
+41 79 542 92 56
+966 563 985 430
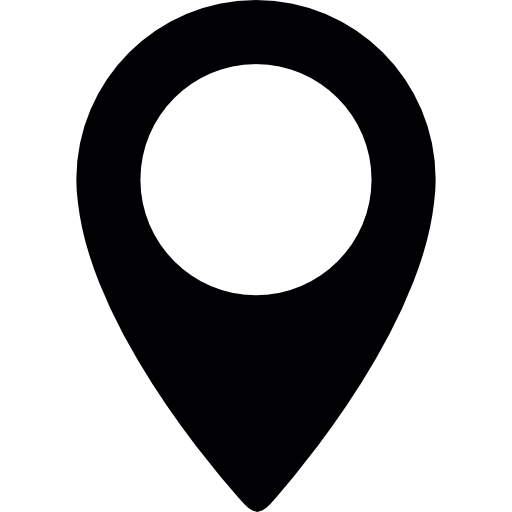
Riyadh, Saudi Arabia
In the world of manufacturing, maintaining consistent product quality is not just a goal—it’s a necessity. Customers demand perfection, regulators enforce strict standards, and businesses must minimize waste to stay competitive. Two critical tools for achieving these objectives are Non-Conformance Reports (NCRs) and Root-Cause Analysis (RCA). Together, they form a powerful framework for identifying, addressing, and preventing quality issues, ensuring that defects are caught early and resolved effectively.
A Non-Conformance Report (NCR) is a formal document used to record instances where a product, process, or procedure fails to meet specified requirements. Whether it’s a defective component, an incorrect assembly, or a deviation from standard operating procedures, NCRs serve as the starting point for quality control investigations.
The primary purpose of an NCR is to:
For example, a pharmaceutical manufacturer might issue an NCR after discovering inconsistent tablet weights during a batch inspection. This documentation ensures accountability and provides a foundation for deeper analysis.
While NCRs identify what went wrong, Root-Cause Analysis (RCA) uncovers why it happened. RCA is a systematic approach to problem-solving that digs beneath surface-level symptoms to identify underlying causes. By addressing the root cause, manufacturers can implement long-term solutions that prevent recurrence.
Common RCA techniques include:
By applying these methods, manufacturers can move beyond quick fixes and implement sustainable improvements.
When combined, NCR and RCA create a robust quality control loop:
For example, a car manufacturer issuing an NCR for a recurring paint defect might use RCA to discover that the spray nozzle design was causing uneven coverage. By redesigning the nozzle and updating maintenance protocols, they eliminate the issue entirely.
Consider a food processing plant struggling with frequent contamination incidents. After issuing multiple NCRs, the quality team conducted an RCA and identified several contributing factors:
Armed with this knowledge, the company implemented targeted solutions:
Within six months, contamination incidents dropped by 70%, leading to higher customer satisfaction and reduced waste.
To maximize the benefits of NCR and RCA, manufacturers should follow these best practices:
Improving quality control with NCR and Root-Cause Analysis is about more than fixing problems—it’s about fostering a culture of continuous improvement. By systematically identifying and addressing issues, manufacturers can reduce defects, enhance customer trust, and achieve operational excellence.
In an era where quality defines brand reputation, companies that embrace NCR and RCA as integral parts of their processes will not only meet expectations but exceed them. These tools are not just mechanisms for solving problems—they are pathways to innovation, efficiency, and sustained success.