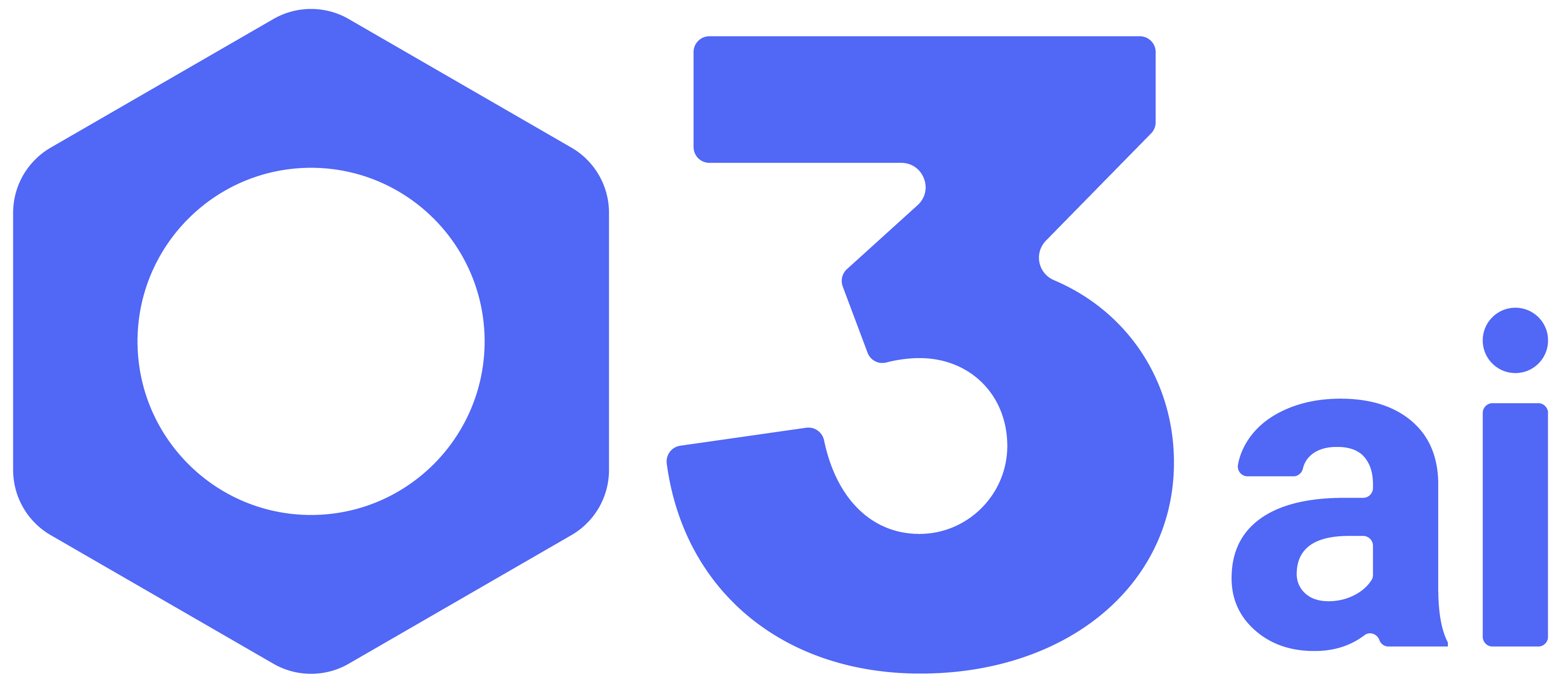
Make Your Factory Lean With O3ai
info@o3ai.com
+41 79 542 92 56
+966 563 985 430
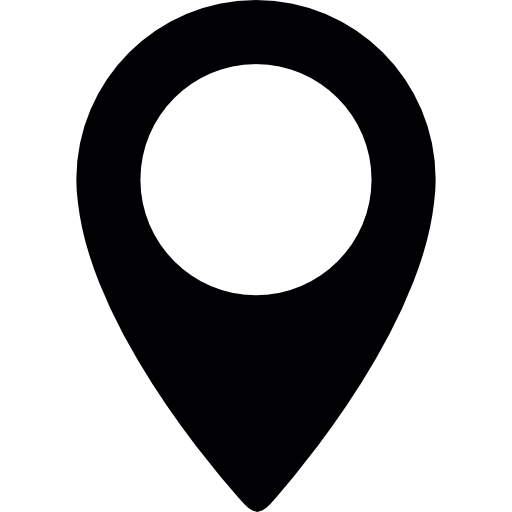
Riyadh, Saudi Arabia
There’s no doubt about it – we’re in a period of global turmoil.
Economic turbulence, war, and a growing energy crisis are causing problems for governments, businesses, and individuals.
Energy shortages and sky-high prices are undermining the economic security and overall stability of the continent.
The energy crisis has its roots in various places – lack of investment in new power plants and renewable energy sources, the outbreak of war in Ukraine, the shutting off of Russian gas pipelines, and the economic aftermath of the COVID-19 pandemic.
As a result, most energy industry experts agree that there is an urgent need to rethink national and international energy production and usage. In recent years, we have seen the rise of Industry 5.0, the principles of which revolve around sustainability, carbon neutrality, circular economy, and energy efficiency.
The manufacturing industry needs to be at the forefront of the drive towards greater energy efficiency, especially when you consider that EU industry accounts for 26% of the total energy consumption in the bloc. The application of Industry 4.0 and Industry 5.0 solutions is key to saving energy in manufacturing.
In this article, we’ll look at some ways in which manufacturing companies can save energy throughout the production process, including the application of cutting-edge digital solutions alongside practical actions.
It may seem obvious, but switching off equipment, heating, and lighting when they are not needed can make a big difference.
For example, powering down computers, photocopiers, and heaters when they are not being used can add up to considerable electricity savings across your entire operations. Heating and air conditioning units are particularly big energy consumers, so the systems should be thermostat or timer controlled, wherever possible. Lighting can be sensor-controlled and fitted with LED bulbs, rather than incandescent or halogen, to minimize energy usage.
Of course, it may not be advisable to shut down all unused manufacturing machines, as the potential energy savings made may be counteracted by the extra power needed to restart the equipment. Therefore, some data analysis may be needed before powering down bigger machines, which we’ll discuss in just a moment.
Reducing the operating pressure of compressed air machinery by just 1-bar can cut energy usage by up to 7%. It’s advisable to switch off air compressors when they are not being used, as the machine may still consume around 70% of its operational energy to maintain the pressure.
Most manufacturing companies use pumps or fans in their production processes. One way to save a large amount of energy is to use highly efficient variable speed motors in your equipment. A 20% reduction in motor speed can halve the total energy used to drive the motor.
O3ai Smart Manufacturing is able to accurately track power parameters and provides insights into the energy consumption of relevant operations and offers role-based prescriptive analytics to take action and prevent waste and optimize energy costs
Most manufacturing companies are moving towards Industry 4.0 solutions to identify and reduce inefficiencies, including energy saving. Smart manufacturing solutions, such as the modules included in the O3ai platform, connect IIoT sensors with the cloud and automatically carry out data analysis to give you the insights you need to become more energy efficient and sustainable.
Data-driven smart manufacturing systems help you to make more informed, and therefore profitable, decisions.
For example, if you want to fit variable speed drives (as mentioned in the previous section), you can apply IIoT and software to collect and analyze the data from machinery that contain motorized fans. Based on the analysis, you can decide whether variable speed motors will be effective in terms of cost and energy efficiency.
Don’t be tempted to use a scatter-gun approach and apply as many cutting-edge digital solutions as possible and hope for the best. This approach rarely works and you may lose out, both financially and in terms of energy efficiency.
The most effective approach is to look at digital solutions through the lens of value engineering.
Here at O3ai, we take a strategic value engineering approach to the implementation of smart manufacturing systems. Our highly-experienced team will carry out an in-depth analysis of your systems and processes, then decide which solutions to implement to get the desirable results.
O3ai’s modular system is ideal if you want to maximize your ROI, without overextending your operational resources and budget.
Our team will set up the overall platform, then add modules one-by-one at different stages of your operations. After the initial consultation and analysis, the process involves carrying out pilot implementations, analyzing the results, before rolling the systems out across your operations. The next step is to start the process again and implement other modules, based on the needs of your business.
To find out more about the O3ai smart manufacturing platform and how we can help you to make large-scale energy savings during these challenging times, book an exploration call today.