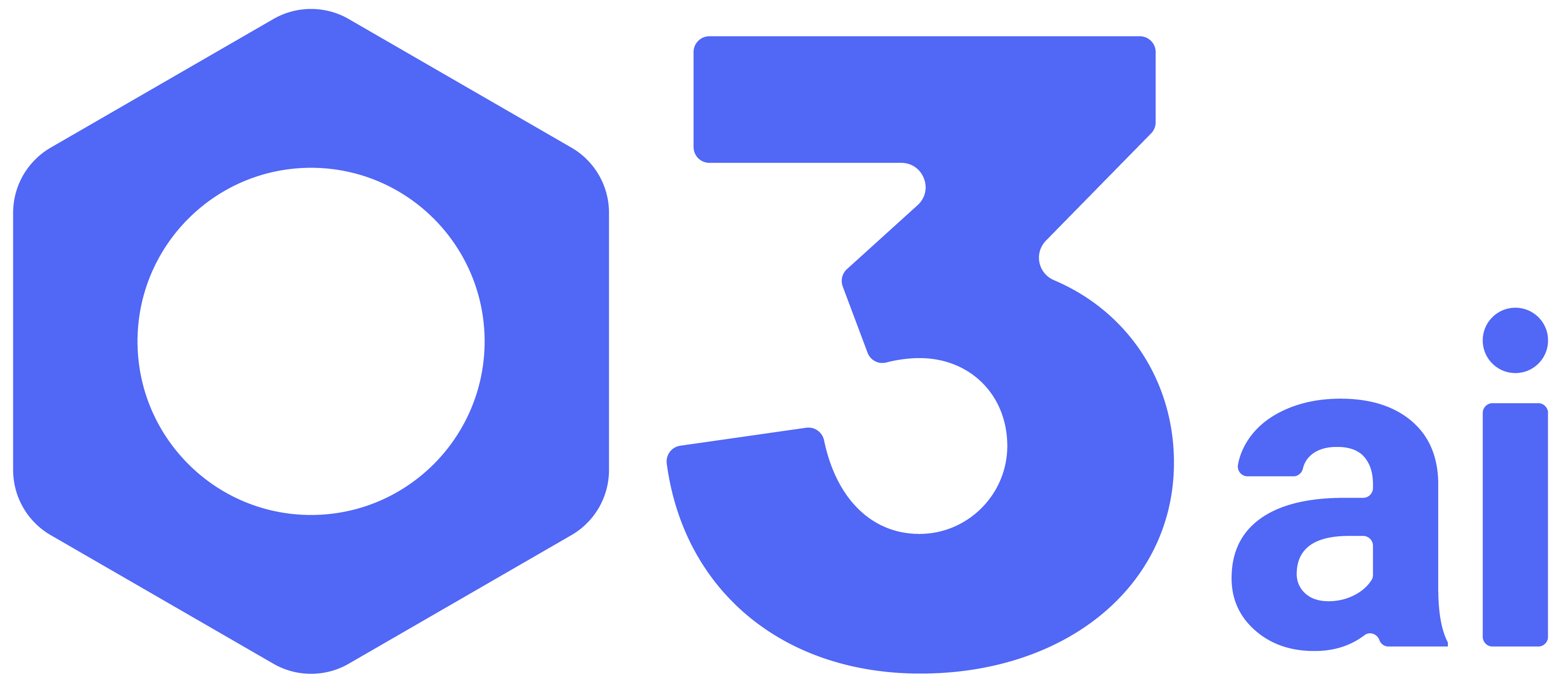
Make Your Factory Lean With O3ai
[email protected]
+41 79 542 92 56
+966 563 985 430
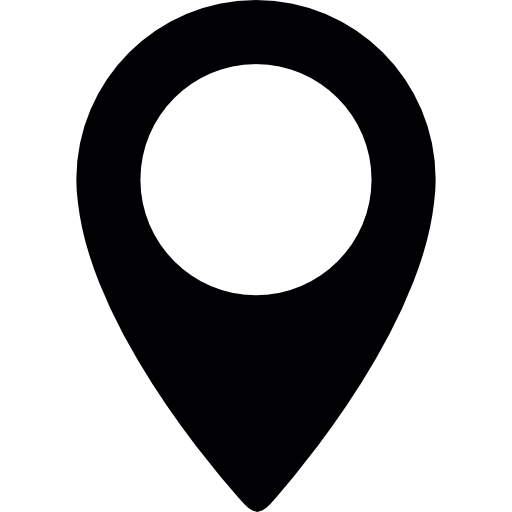
Riyadh, Saudi Arabia
The digital transformation is progressing steadily, also in the manufacturing industry and in industrial production. The big driver for this change is the interconnectedness of machines or systems, processes and people, and the associated collection and optimization of data of all kinds. The new industrial manufacturing is a digital enterprise that is networked and connected, flexible, agile and smart.However, many companies still don't know how to address this issue and are hesitant to tackle digital transformation because they don't know where to start. What to do and how to add real value operationally and strategically?
Based on our experience, there are best practices and steps for this with manageable effort to get started with digital transformation in manufacturing and if you are looking for ways to improve your operations and see positive results quickly, below are some steps you can take immediately.
What comes to mind is the concept of the Digital Twin, a real-time digital replica of a physical object or processes that helps optimize production performance.
Until recently, the digital twin - and the vast amounts of data it processes - was often difficult for both SMEs and large enterprises to access due to the limitations of digital technology and the prohibitive costs of data processing, storage and bandwidth.
However, these barriers have been drastically reduced in recent years, and today, for example, there is a cloud solution from O3ai that not only enables the creation and use of a Digital Twin to virtually simulate a shop floor and production lines in the shortest possible time but also actively takes the best and most appropriate actions to optimize processes (e.g., when a piece of equipment is operating outside defined tolerances) thanks to advanced AI modeling and machine learning.
So why is the Digital Twin so important, and why should companies consider it in for the shop floor and production lines?
The Digital Twin can enable companies to have a complete digital footprint of their products from design and development to the end of the product lifecycle. This, in turn, can allow them to understand not only the product as it is, but also the production systems and associated processes used to make the product.
By creating a Digital Twin and using advanced analytics, companies will be able to plan better and solve physical problems faster by identifying them earlier and predicting outcomes with a much higher degree of accuracy. With this type of smart manufacturing, companies can streamline operations, reduce downtime and lower maintenance costs, and generally increase operational efficiency.
A Digital Twin delivers quick wins:- Capacity Increase- Reduction in Downtime Events- Better Planning Efficiency - Maintenance Cost Reduction- Inventory Reduction - Overall Equipment Effectiveness (OEE)
Now, it can be a daunting task to create a Digital Twin and every company is different and has its own challenges accomplishing this task. O3ai Smart has designed a end-to-end software solution with these challenges in mind to provide a user-friendly experience that allows users to get the most out of their data, regardless of what sensors and sources (real-time and operational) it comes from and where it is located or how it is structured.
Book Your Free Exploration Call
Want to take your optimization efforts to the next level? We'll walk you through our O3ai Smart Manufacturing software, discuss your goals and challenges, and provide initial recommendations on how we can help you realize your own Digital Twin.