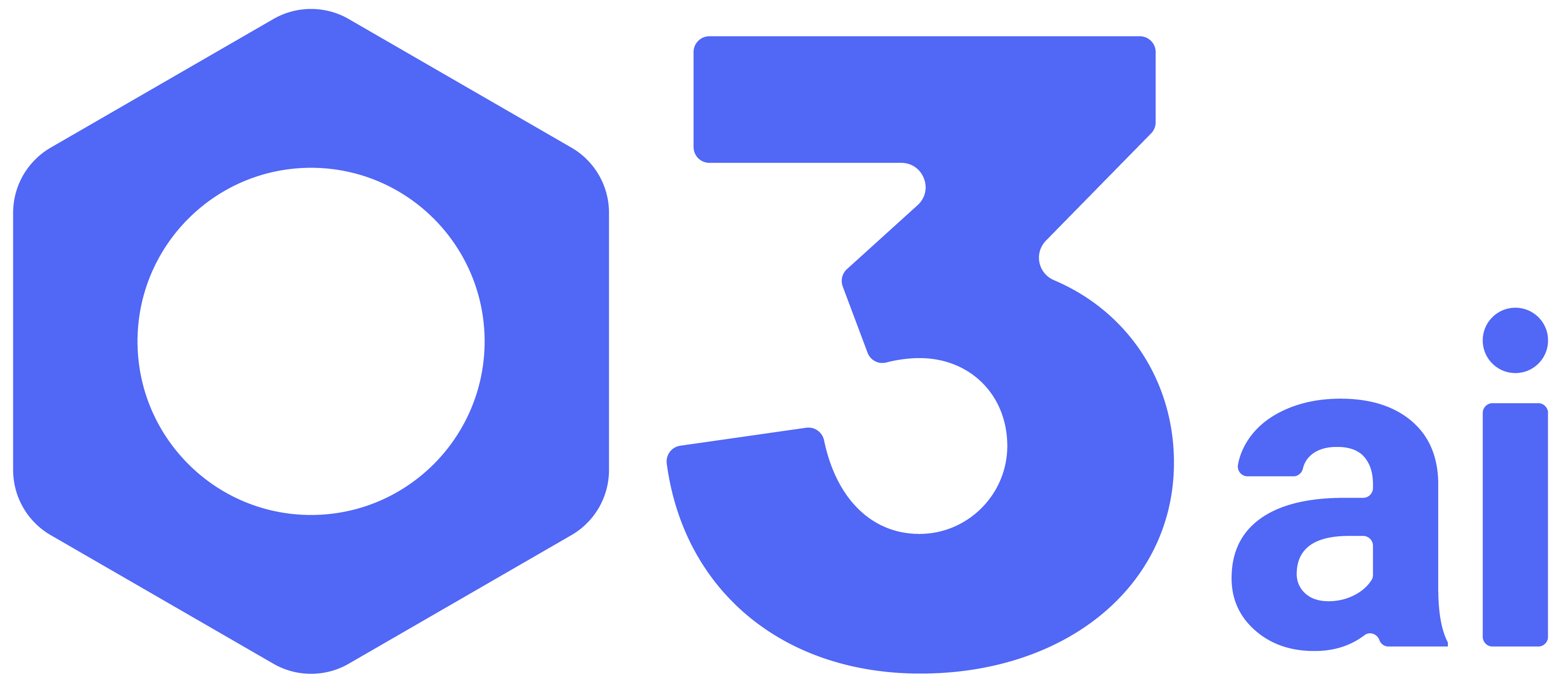
Make Your Factory Lean With O3ai
info@o3ai.com
+41 79 542 92 56
+966 563 985 430
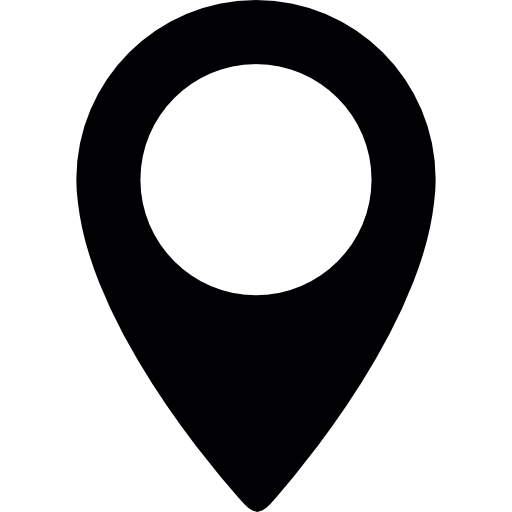
Riyadh, Saudi Arabia
The smart manufacturing revolution is here, transforming industries and unleashing a wave of innovation. But with great progress comes a unique set of workforce challenges that need to be tackled head-on.
In this article, we'll reveal the top workforce challenges in smart manufacturing and unlock powerful solutions to help you conquer them and maintain a cutting-edge advantage.
At the 2023 World Economic Forum (WEF) in Davos, 75% of global companies surveyed reported that they faced talent shortages, profoundly impacting staff upskilling and retention rates.
The manufacturing sector has often been seen as less alluring than other tech-driven industries, making it harder to attract and retain the best and brightest. This is especially true in our current age of labor shortages. Now is the time to mobilize your troops for action and get the right people on the frontline.
Attract talented individuals by highlighting the ground-breaking smart manufacturing technology that you use and emphasize the boundless opportunities for growth and development within your business. Offer irresistible salaries, flexible work arrangements, and ample opportunities for professional growth to keep top talent engaged.
Tesla, an electric vehicle and clean energy company, has successfully attracted and retained top talent by showcasing its commitment to innovation and sustainability. The company not only offers competitive salaries and benefits, but also provides a unique workplace culture that fosters creativity and collaboration. Tesla's Gigafactory, for example, is an advanced manufacturing facility that features cutting-edge technology and smart manufacturing processes, making it an appealing workplace for ambitious professionals. By focusing on innovation and growth, Tesla has positioned itself as an attractive employer in the smart manufacturing space.
The convergence of technology and traditional manufacturing practices has given rise to a significant skills gap. In today's fast-paced world, the workforce must possess a blend of technical expertise and analytical acumen to keep up with the ever-changing industry demands. It's crucial for companies in the smart manufacturing sector to recognize this challenge and adopt proactive measures to ensure their workforce is prepared to navigate the constantly evolving landscape.
Form strategic partnerships with educational institutions and industry experts to develop specialized training programs and certification courses. This approach will help you cultivate a skilled workforce that's ready to tackle the challenges of smart manufacturing head-on.
Here at O3ai, we are creating a variety of resources and materials to help bridge the skills gap. We have several experts on-board, including Masood Hassan who is a digital operations specialist. We also have a team of experienced engineers to help you plan, implement, and adopt smart manufacturing technology in your factory.
We will also be launching O3ai Lite shortly, which is a perfect first step towards smart factory success. O3ai Lite has all the main modules you need to get started with smart manufacturing, but without putting too much strain on your operations and workforce. Contact us to receive updates on O3ai Lite and when it will be launched.
In the lightning-fast world of smart manufacturing, skills can become obsolete in the blink of an eye. Companies must nurture a culture of relentless learning and adaptability to stay on the cutting edge.
Invest in continuous employee training, professional development programs, and knowledge-sharing initiatives to keep your workforce abreast of the latest industry trends and best practices.
Bosch, a global leader in engineering and technology, has demonstrated its commitment to cultivating a culture of non-stop learning by establishing the Bosch Training Center. This state-of-the-art facility offers a wide range of training courses and programs designed to equip employees with the skills and knowledge necessary to excel in the smart manufacturing industry.
In addition to technical training, Bosch also encourages employees to engage in cross-functional learning and collaboration through internal conferences, workshops, and online resources. This comprehensive approach to continuous learning not only helps Bosch employees stay up-to-date with industry trends but also fosters a culture of innovation and adaptability within the company.
A diverse workforce is a treasure trove of fresh perspectives and ingenious solutions. In an industry as dynamic as smart manufacturing, diversity is the secret ingredient to staying ahead of the competition.
Deploy diversity and inclusion initiatives to attract talent from diverse backgrounds. Provide equal opportunities, foster a culture of respect, and ensure that company policies are inclusive and supportive of all employees.
IBM, a multinational technology and consulting company, has long been a champion of workforce diversity in the technology sector. The company has implemented a wide range of diversity and inclusion initiatives to ensure its workforce is as diverse as the clients they serve.
IBM has established several affinity groups, such as Women at IBM, IBM Black Network, and IBM Pride, to provide support, networking, and professional development opportunities for employees from diverse backgrounds. In addition to these internal initiatives, IBM actively partners with organizations like the Society of Women Engineers and the National Society of Black Engineers to expand its talent pipeline and attract diverse candidates.
Moreover, IBM has consistently ranked as a top employer for working mothers and has received numerous awards for its commitment to diversity and inclusion, including the Catalyst Award, which recognizes companies that excel in advancing women in the workplace.
Smart manufacturing companies must strike the perfect balance between technology and human resources. Workforce optimization is critical to boosting productivity and trimming costs.
Embrace data-driven workforce management solutions to optimize labor allocation and scheduling. Utilize analytics to pinpoint areas of improvement and harness automation to streamline repetitive tasks, freeing up your workforce to focus on high-impact activities.
The Liquid Packaging Company, a manufacturer of packaging solutions, faced challenges in productivity, quality management, and increasing customer complaints. To tackle these issues, the company turned to O3ai Smart, a smart manufacturing platform that enabled them to optimize their workforce and improve overall efficiency.
With the deployment of O3ai Lean Apps, The Liquid Packaging Company digitalized and standardized its Autonomous and Predictive Maintenance (AM, PM) Safety, Quality, and Production processes across the plant. The platform allowed them to:
In conclusion, tackling workforce challenges, such as the growing skills gap, in smart manufacturing is the key to unlocking success. By proactively addressing these challenges and implementing the right solutions, you can assemble a formidable workforce ready to dominate the ever-evolving landscape of smart manufacturing. Equip your team with the right tools and watch your company skyrocket to new heights.
For assistance in overcoming workforce challenges in this new and exciting age of smart manufacturing, get in touch with one of our expert team members at O3ai today.