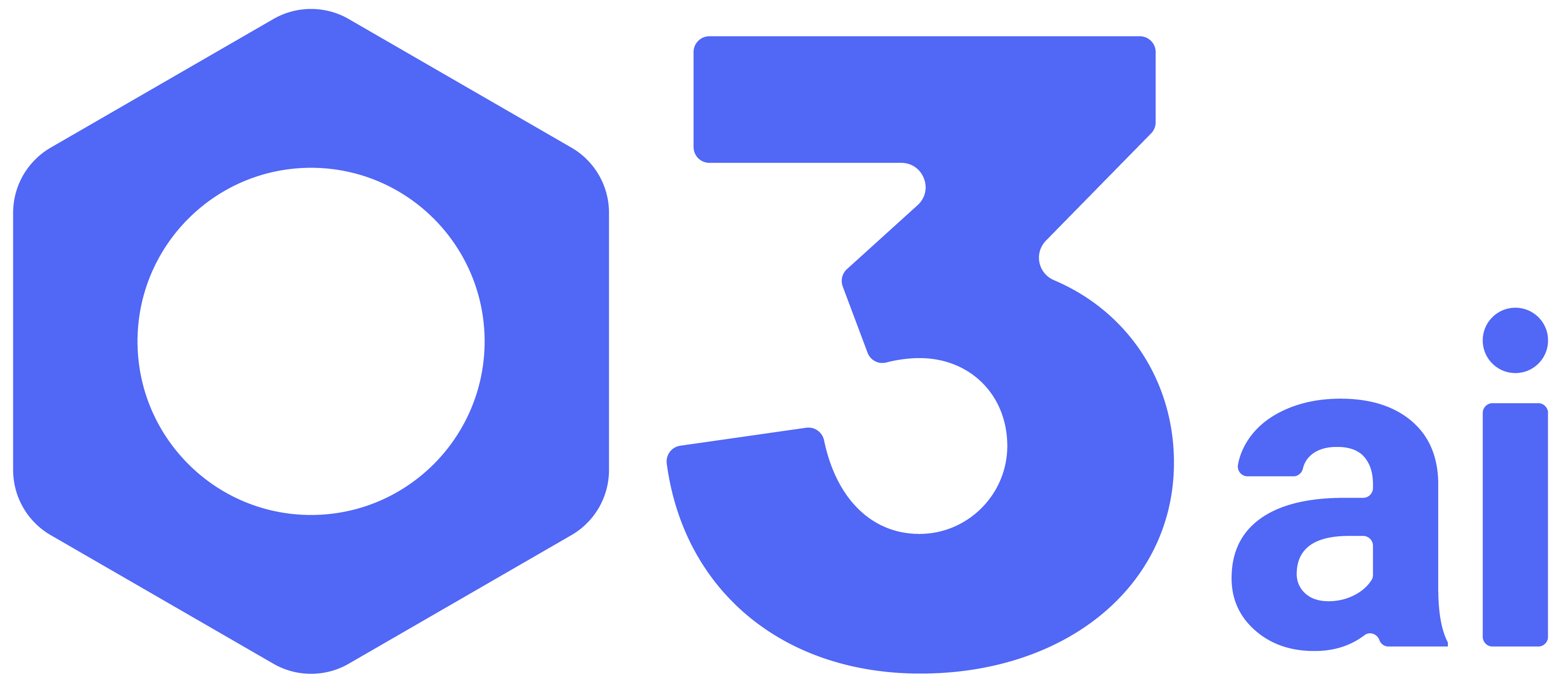
Make Your Factory Lean With O3ai
info@o3ai.com
+41 79 542 92 56
+966 563 985 430
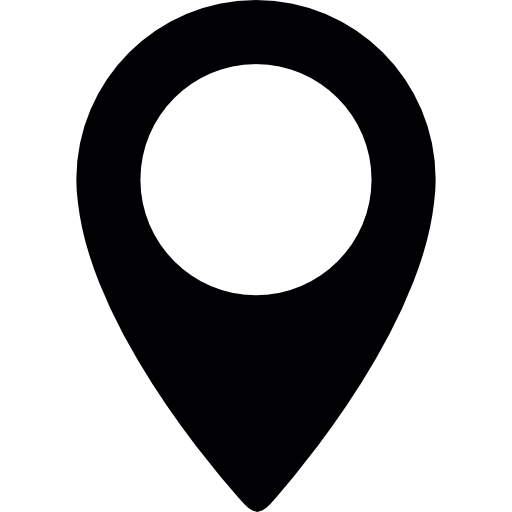
Riyadh, Saudi Arabia
In today’s hyper-competitive manufacturing landscape, maintaining consistent quality is no longer a one-time effort—it’s an ongoing commitment. Continuous Quality Monitoring (CQM) has emerged as a game-changing approach, enabling manufacturers to detect issues in real time, prevent defects, and ensure compliance with ever-evolving standards. By embedding quality into every stage of production, companies can reduce waste, enhance customer satisfaction, and drive operational excellence. Here are the best practices to master Continuous Quality Monitoring.
The foundation of effective CQM lies in real-time data collection. Modern technologies like IoT sensors, machine vision systems, and automated inspection tools provide instant feedback on product quality and process performance. For example:
By capturing data continuously, manufacturers can identify trends, spot anomalies, and intervene before small issues escalate into major problems.
Continuous monitoring is only as effective as the actions it triggers. Automated alerts ensure that teams are immediately notified when quality thresholds are breached. For instance:
This proactive approach minimizes downtime, reduces rework, and ensures faster resolution of quality issues.
Quality should not be an afterthought—it must be embedded throughout the production process. Best-in-class manufacturers adopt a “quality by design” philosophy, where quality checks are integrated at every stage:
This layered approach ensures that defects are caught early, reducing the cost and complexity of corrections.
Predictive analytics takes Continuous Quality Monitoring to the next level by forecasting potential issues before they occur. By analyzing historical and real-time data, manufacturers can identify patterns that indicate future risks. For example:
Predictive insights enable manufacturers to shift from reactive problem-solving to proactive prevention, saving both time and resources.
Continuous Quality Monitoring is not just about technology—it’s about people. To succeed, organizations must foster a culture where everyone takes ownership of quality. Key strategies include:
When employees understand their role in maintaining quality, they become active participants in driving continuous improvement.
Consistency is key to effective CQM. Standardizing processes ensures that quality checks are performed uniformly, regardless of location or operator. Documenting procedures also provides a reference point for training and audits. For example:
Standardization reduces variability, making it easier to identify and address deviations.
To sustain success, manufacturers must regularly evaluate the effectiveness of their CQM efforts. Key performance indicators (KPIs) such as defect rates, first-pass yield, and customer complaints provide valuable insights into quality performance. Regular reviews help identify areas for improvement and ensure that CQM initiatives remain aligned with business goals.
For instance, a manufacturer might discover that while defect rates have decreased, customer complaints about late deliveries have risen. This insight could prompt a review of supply chain processes to balance quality with timeliness.
A leading electronics manufacturer implemented Continuous Quality Monitoring across its global facilities. By deploying IoT-enabled sensors and predictive analytics, they achieved remarkable results:
The company attributed its success to a combination of real-time monitoring, predictive analytics, and employee engagement, proving that CQM is a holistic endeavor.
Continuous Quality Monitoring is more than a strategy—it’s a mindset. By leveraging real-time data, predictive analytics, and standardized processes, manufacturers can create a robust framework for maintaining excellence. However, the true power of CQM lies in its ability to unite technology and people, fostering a culture where quality is everyone’s responsibility.
In an era where customers demand perfection and regulators enforce strict compliance, Continuous Quality Monitoring is not optional—it’s essential. By adopting these best practices, manufacturers can not only meet expectations but exceed them, positioning themselves as leaders in their industries. Quality is no longer a destination; it’s a journey, and CQM is the roadmap to success.