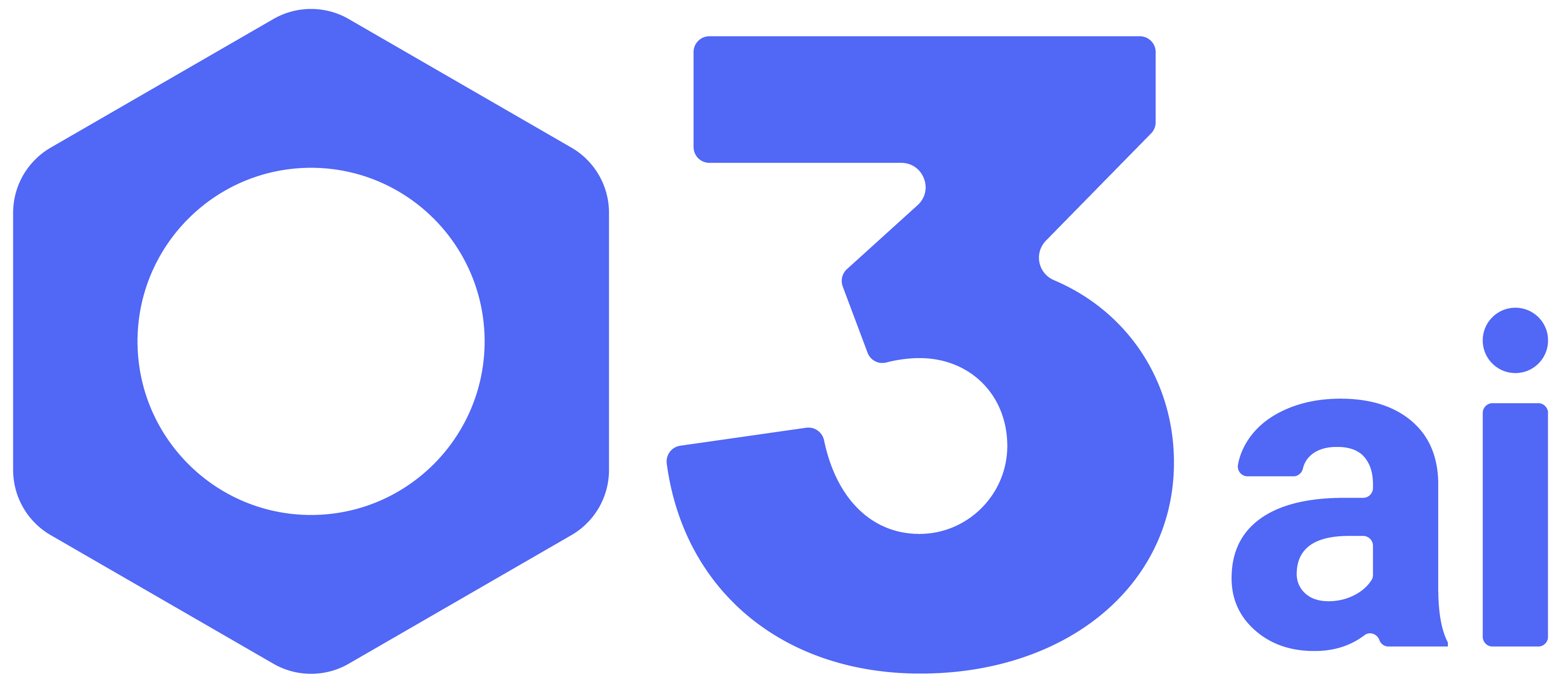
Make Your Factory Lean With O3ai
info@o3ai.com
+41 79 542 92 56
+966 563 985 430
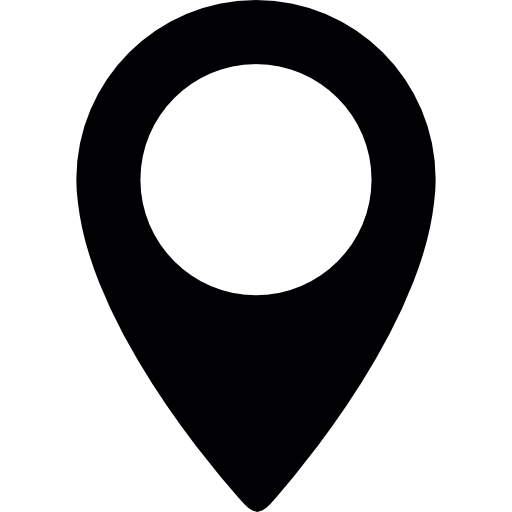
Riyadh, Saudi Arabia
Manufacturers often struggle to pinpoint the exact cause of production issues. Traditional problem-solving methods rely on historical data and manual analysis, leading to delays, recurring defects, and inefficiencies. AI-driven real-time root cause analysis is transforming this approach by delivering instant insights, allowing manufacturers to resolve problems before they escalate.
“AI-driven insights allow businesses to move beyond reactive problem-solving, transforming quality control and operational efficiency in real-time.” – PwC, AI in Industrial Operations Report
Instead of waiting for failures to impact productivity, AI-driven analytics enable manufacturers to detect patterns, prevent disruptions, and enhance efficiency through automated decision-making.
Conventional root cause analysis (RCA) methods, such as Fishbone Diagrams and 5 Whys, often rely on human judgment, making them time-consuming and prone to bias. These manual approaches have several limitations:
A Deloitte study on smart manufacturing found that 67% of manufacturers still rely on manual RCA methods, leading to an average resolution time of 36 hours per issue—a costly delay that AI can drastically reduce.
AI-powered RCA moves beyond traditional methods by leveraging machine learning, predictive analytics, and real-time monitoring to analyze vast datasets instantly. Instead of relying on post-event reports, AI systems continuously track production variables, detect hidden correlations, and suggest corrective actions in seconds.
AI constantly monitors production processes and identifies deviations in real time.
AI connects different data points—temperature, pressure, machine speed, and operator actions—to uncover the root cause of inefficiencies.
By analyzing historical and live data, AI forecasts potential breakdowns and enables preventive action.
Beyond identifying issues, AI provides data-backed corrective actions, helping operators address problems faster.
According to McKinsey & Company, AI-enabled analytics deliver:
✔ Up to 50% faster issue resolution
✔ 30-40% reduction in equipment downtime
✔ 25% lower defect rates and rework costs
These benefits make AI-powered RCA not just an operational tool, but a strategic advantage for manufacturers aiming for greater efficiency and cost reduction.
For companies looking to integrate AI-driven RCA into their operations, a structured approach is key:
✔ Connect AI to MES & IoT Systems – Ensure AI has access to real-time production data.
✔ Leverage Cloud & Edge Computing – AI should process data on-site (edge computing) or through cloud-based platforms.
✔ Train Teams on AI Insights – Ensure operators and engineers understand and trust AI-generated recommendations.
✔ Start Small, Scale Gradually – Test AI on one production line before expanding company-wide.
At O3ai, our AI-driven manufacturing intelligence platform enables manufacturers to detect and resolve production issues instantly.
🔹 Instant Fault Detection – AI continuously scans production lines, identifying anomalies in real time.
🔹 Predictive Failure Warnings – O3ai forecasts potential breakdowns before they impact operations.
🔹 Automated RCA Reports – Actionable insights are delivered through intuitive dashboards.
🔹 Seamless Integration – O3ai connects with MES, IoT, and ERP systems for a holistic quality management approach.
By adopting O3ai’s AI-powered RCA, manufacturers experience fewer defects, reduced downtime, and maximized efficiency, ensuring they stay ahead in an increasingly competitive market.
Manufacturers no longer need to rely on slow, manual methods to find the root cause of production issues. AI-powered root cause analysis is eliminating guesswork, reducing delays, and improving decision-making across production lines.
With platforms like O3ai, manufacturers can seamlessly integrate AI-driven RCA, boosting operational efficiency, preventing costly failures, and driving continuous process improvements.
Transform your factory with real-time AI insights—contact O3ai today.