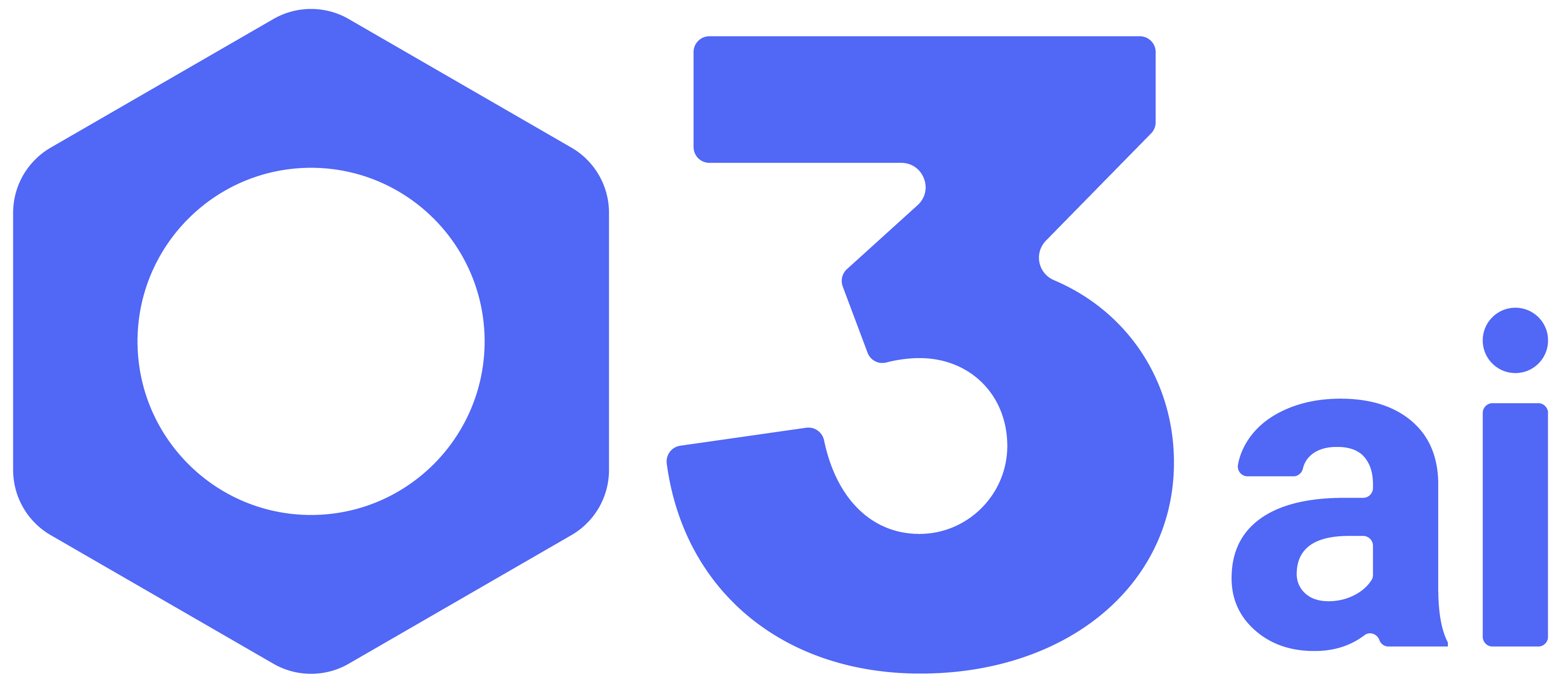
Make Your Factory Lean With O3ai
info@o3ai.com
+41 79 542 92 56
+966 563 985 430
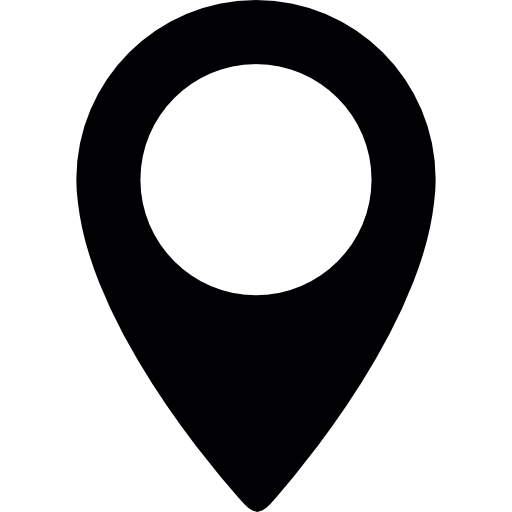
Riyadh, Saudi Arabia
Predictive maintenance is a holy grail for manufacturers:
The ability to predict when machines are going to fail and take preemptive action to prevent downtime.
Industry experts agree unanimously that predictive maintenance has the potential to save manufacturers a lot of money. It ensures more consistent productivity levels and cuts down on overall repair and replacement costs.
But where do you start when trying to implement a predictive maintenance program?
The following 5 steps will get you to think deeply about your overall maintenance strategy and implement it successfully.
Before you start creating a plan and spending money on technology, you need to get a firm grip of what predictive maintenance actually is and what it means for your business.
The best place to start is to define predictive maintenance alongside some other maintenance strategy types, by way of comparison.
Once you have a firm understanding of what predictive maintenance is, the next step is to identify how it can enhance your manufacturing operations.
Let’s imagine that you have a set of three CNC milling machines that are in almost constant use. You also have a CNC lathe that is used infrequently. If one milling machine breaks down it can slow down your entire production process. Therefore, any predictive maintenance technology that you implement should probably be applied to the milling machines first. Make sure that you keep your goals realistic, for instance you may set a goal to reduce the average downtime of each milling machine by 30% in the first year.
The first stage of predictive maintenance implementation is to gather data from the relevant machines, either through the use of built-in technology or through the addition of IoT sensors such as vibration sensors, temperature sensors, or imaging technology.
Next, the data needs to be connected to your local network or the cloud. At o3, we have defined four maturity levels of connectivity:
Once there is a system in place to collect the data, you need to find a way to process it and analyze it. A modular smart manufacturing platform such as o3 allows you to install a specialist predictive maintenance module that acts as a digital twin.
The module has a range of built-in statistical predictive models to choose from. Machine learning algorithms will learn from your dataset to improve the model and automatically recommend maintenance tasks based on the results.
As a first step, you may want to consider O3ai's autonomous maintenance module, which assists operators in carrying out basic preventive maintenance and managing defects. It's the perfect foundation for smart management of maintenance.
The purpose of a predictive maintenance program is to automatically monitor your machines, analyze the data, and alert you when you need to take action. Therefore, you need to configure the system to alert you when data anomalies are found or parameters reach certain levels.
You can configure the system to send notifications to operators and maintenance technicians through mobile devices. They can also view automated task instructions on their device and access key information and specifications. The whole process will be streamlined.
The high level of automation throughout the system allows you to fully optimize your machine maintenance. From data capture and processing to insight generation and alerts – each step is automated.
At o3, we have a supply chain and value engineering expert in our team who can help you to identify the key areas to implement smart solutions.
If you’re interested in finding out more about o3 smart manufacturing and how we can help you to implement predictive maintenance in your business, get in touch and book a demo.